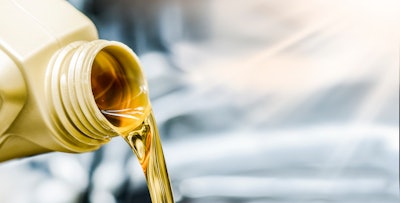
Changing oil in cold weather can take a toll on both machines and people. Working in subzero conditions quickly induces fatigue. As the ambient air temperature drops, oil thickens and equipment becomes more reluctant to turn over due to the increased oil friction resistance and decreased battery efficiency.
The right procedures, fluids and equipment make all the difference. Here are some tips for changing oil in the cold.
Select the right viscosity
Oil viscosity measures the resistance of the oil to flow at different temperatures, ultimately determining the thickness or thinness of the oil. This is one of the most important properties of oil because viscosity provides the lubrication film between metal parts. The oil needs to be thick enough to prevent metal contact while being thin enough to prevent excessive energy loss.
Temperature changes influence oil viscosity, which makes changing oil in cold weather more difficult. You’ll need the right oil to match the conditions. The oil must remain sufficiently viscous at high temperatures, but it can’t be too thick at low temperatures. It also must remain robust across a wide temperature range to handle cold starts in the winter and normal internal operating temperatures.
When selecting the appropriate oil, pay particular attention to the number before the W in the oil specification. That number is the winter viscosity. A lower number means it is more fluid at a colder temperature. For instance, a 5W-40 engine oil is thinner in cold temperatures than a 10W-30.
Since viscosity depends on temperature, consult the equipment owner’s manual and make sure you use the recommended oil for the temperatures you will be operating in. Equipment operator manuals may suggest different oils for varying temperature ranges.
Always warm engines
Never perform "cold" oil changes, regardless of the weather outside. Oil should always be warm so it flows freely and drains completely.
Start the engine and warm it up to normal operating temperature to circulate the oil prior to the oil change or perform the oil change shortly after the equipment has been shut down for the day. Running the engine immediately before an oil change also helps ensure better removal of contaminants from inside the engine. Contaminants from wear, the combustion process and the environment are suspended in the oil when the machine is working.
Shortly after shutting the machine down, these contaminants settle out to internal surfaces and the bottom of the oil pan. If you change the oil after the engine has been at rest, these contaminants will likely adhere to the internal engine surfaces.
Choose the right equipment
When equipment is integral to a jobsite’s overall operation, the time and cost to transport equipment to the shop and back results in lost productivity. This can quickly erode revenue potential.
It is often more cost effective to service equipment on the jobsite, even in cold weather. Mobile preventive maintenance solutions can give you a leg up on the competition, but make sure that your mobile lube solution is set up to protect vital assets—your technicians and your equipment—as the temperatures drop.
Working long hours to finish changing oil in cold weather can be unbearable with a subpar lube truck setup. Using buckets to change oil further complicates the task and exposes technicians to hot oil. The right tools for the job make all the difference.
Using a closed-loop system with quick disconnects protects your technicians from oil exposure and reduces manual effort while your technicians battle the weather. Less physical effort in subzero temperatures means more productive technicians.
Enclosed trucks, enclosed vans, enclosed trailers or even a custom system can also simplify changing oil in cold weather. Heated fluid tanks that use immersion heaters can increase productivity. Coolant circulates through probes in these tanks, transferring heat to the oil and enabling easier oil changes as outside temperatures plummet.
The right tools for the job will make life a lot easier for your technicians and equipment.